Reach Out to Us
Industry leader in manufacturing professional-grade tools and equipment
Ingersoll Rand is a global leader in innovative design and production of high-quality power tools for manufacturing, assembly, construction, and automotive industries. For more than 125 years, professionals across industries have trusted our tools and systems to deliver unparalleled performance and reliability. Our advanced engineering and manufacturing have a standard of excellence often copied, but never matched.New Products
Solutions We Provide
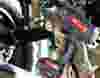
Assembly Solutions
Discover Ingersoll Rand's range of high-precision assembly tools, including corded DC, transducerized systems, and durable non-transducerized solutions.
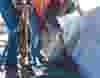
Construction Tools
Trying to find the right construction tools for your company? Ingersoll Rand is one of the oldest names in the industry
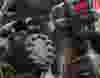
Drilling and Bolting Tools
From the hardest-hitting impact wrenches in the business to ratchets with innovative ergonomic designs, our tools are specifically engineered with performance in mind – making your job easier and more productive.

Engine Starters and Air Motors
Explore top-tier Ingersoll Rand Engine Starters and Air Motors designed for unmatched reliability and performance. Discover our durable, efficient solutions for your power needs today.
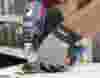
Surface Preparation and Finishing
Explore top-tier surface preparation and finishing tools with Ingersoll Rand. From sanders to grinders, find durable, high-performance tools designed to give your projects a flawless finish.
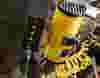
Lifting Solutions
The Latest from Ingersoll Rand Power Tools
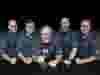
Our Legacy of Excellence Recognized in Popular Mechanics 2025 Tool Awards
Ingersoll Rand's legacy of engineering excellence has been celebrated with the W7153 IQV20™ DXS® Cordless Impact Wrench and the H3111 20V Cordless Heat Gun being honored as Best Power Tools in Popular Mechanics 2025 Tool Awards. The acclaim from these awards brings attention to our focus on...
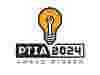
Celebrating Excellence: Ingersoll Rand® Tools Win 2024 Pro Tool Innovation Awards
Explore the award-winning Ingersoll Rand® tools honored at the 2024 Pro Tool Innovation Awards for their outstanding design and performance in the vehicle services industry.
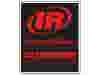
Air Power (NC) Expands Distribution Network to Texas, Oklahoma, and Louisiana
Air Power Manufacturing Solutions (North Carolina), a longstanding and trusted distributor of Ingersoll Rand Power Tools & Lifting, is preparing to extend their services into the states of Texas, Oklahoma, and Louisiana...
Industries Served
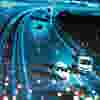
Automotive and Transportation
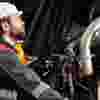
Industrial Equipment
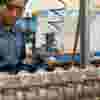
Industrial Assembly
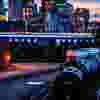